Rotary evaporation is a method used in chemical laboratories for efficient removal of solvents by distributing it as a very thin film on the interior vessel at low pressure and temperature. The rotatory evaporator is designed to work under a vacuum; to lower the boiling point of molecular compounds and heating the sample at the same time. To understand the rotary evaporation method, you need to know the main parts of a rotary evaporator and its functions as well as the rotovap working principles of the different parts.
>> Rotary Evaporator Definition
Rotary Evaporator Parts and Functions
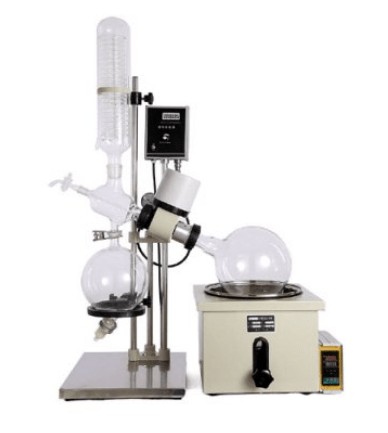
1. Rotary motor.
This is an electric-powered motor used for rotating the evaporation flask at a continuous and constant speed. This results in an increased surface area for evaporation per unit time as well as even mixing and heating hence a stable and even evaporation.
2. Heating bath.
This can be either a water or oil bath The mainly used heating bath is a hot water bath. The function of the heating pot is to heat the sample and help in temperature regulation.
3. Vacuum source.
This is the system responsible for creating a vacuum within the airtight set-up, thereby reducing the pressure within the system. The vacuum source can be simply a water aspirator consisting of a water immersed trap, or a complex mechanical vacuum pump consisting of a refrigerated trap.
4. Glass tube.
The glass tube has two functions, the first is to protect and support the sample during rotation while the second is to help in the creation of a vacuum.
5. Condenser.
The condenser consists of a coil where the coolant passes through. In the condenser, the evaporated vapor is chilled and condensed back to liquid.
6. Receiving flask.
The function of the collecting flask is to receive the distilled sample.
>> Rotary Evaporator Parts and Their Functions
Rotary Evaporation Method
The method of evaporation used in a rotary evaporator is mainly based on two main components of the rotavap: vacuum evaporation, which allows evaporation of components at low pressure and temperatures, and the rotation of the evaporating flask, that increases the surface area for evaporation per unit time as well as enhancing forced convection thereby allowing even mixing and stable evaporation.
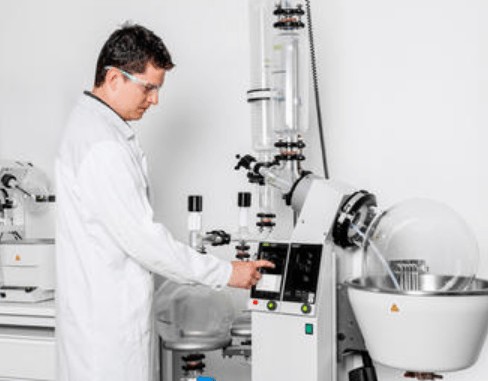
The following are the steps on how to commence rotary evaporation;
- Heat the water bath and let the condenser get cold. The inverse of this will lead to sub-optimal results.
- Make sure you tighten the clamps of the bump trap and sample flask.
- Rotor activation which should spin at a high speed enough to create a thin inner layer on the evaporating flask.
- Activation of the vacuum pump followed by closing the stopcock.
- Occasionally keep checking whether everything is going on well during the process and if there is any case of bumping open the stopcock.
The following are the steps on how to shut down rotary evaporation;
Shutting down a rotary evaporator is a step-wise procedure so as to avoid undesired outcomes.
- Start by removing the flask from the water heat bath.
- Turn off the motor.
- Hold the flask with your right hand and open the stopcock with your left hand.
- Remove the evaporating flask to obtain the residue and collect the distillate from the receiving flask.
- Switch off the vacuum source, the condenser, and the water bath.
The omission of any step during halting of the rotary evaporator will lead to unwanted outcomes.
Besides been a single sample natured system there are advantages of using this system in extraction and distillation as it suppresses bumping-this is the tendency of solvents with high boiling points to accentuate. It also results in the formation of a warm thin film that spread over the surface this is due to frictional and centrifugal force between the rotating flask and the wall.
Great care should be taken to avoid damaging the pump and release toxic volatile compounds into the atmosphere. If the rotary evaporator is in the right position it’s advisable to vent in a fume hood or attach a scrubber full of paraffin oil to avoid inhalation of toxic gases.