What Is A Jacketed Agitated Glass Reactor?
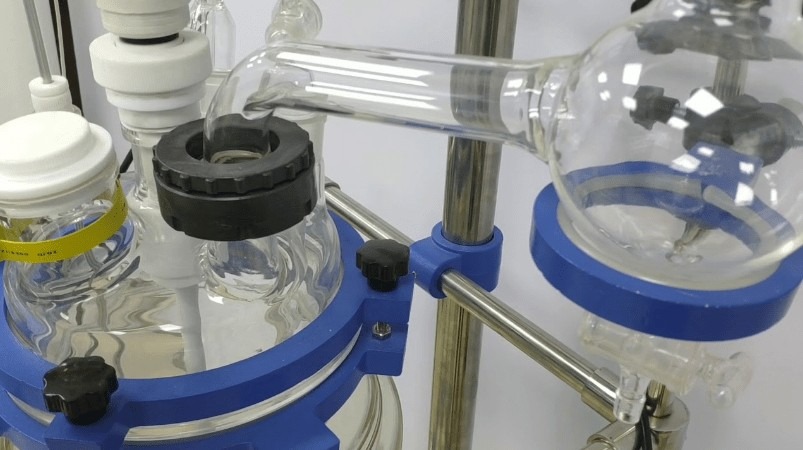
Many know that a glass reactor is a form of a chemical reactor to realize the process industry. A jacketed reactor is designed to control the temperatures of its contents with a heating or cooling jacket around the reactor. The jacket can permit a uniformed exchange of heat between the walls of the vessel and the fluid circulating in it.
On the market today, there are several jacketed reactors, all with their own unique features. As a chemical reactor, the jacket type is always used to remove the elevated heat of reaction or reduce the viscosity of high viscous fluids. Cooling jackets have a very important role. This type of jacket has the ability to stop the upward spiral of hot temperatures that are responsible for increasing the rate of reaction. This reaction would produce more heat, so the cooling liquids flow through the jacket and collect heat energy from the outer surface.
Agitation in glass reactors is also very important and can improve the homogeneity of the fluid properties. The fluid properties include the temperature and concentration, and the agitation refers to putting it into motion by stirring or shaking to achieve mixing. A jacketed reactor is used in many fields such as chemical, food, dyes, and drug industries.
Benefits of Using Jacketed Agitated Reactor
There are many advantages to using a jacketed reactor:
- It will provide a higher volume of flow overall due to the pressure drop through a zone that is lower than if the complete jacket is a single-zone
- It has the ability to direct flow to specific portions of a jacket
- These units are space savers
- They are leak-free vessels
- The jacketed reactor is easy to use
- You achieve more reactions in less time
- They provide a maximum chemical resistance
- They have a wide temperature and pressure range
- These units upgrade to automation
- These units are reliable and robust
The composite construction of metal and glass provide a lot of benefits. The external steel construction of the reactor provides strength. The internal glass lining provides universal corrosion protection along with a smooth, non-contaminating surface.
During the process of fabricating the glass to the lined steel equipment, fuses the glass to the steel. The bond is incredibly strong. The result of this construction is corrosion resistance to bases and acids, as well as being able to withstand high operating temperatures and pressures. The structure of this vessel will also give you the ability to add or remove heat to your batch.
The Different Jacketed Agitated Glass Reactor and Their Applications
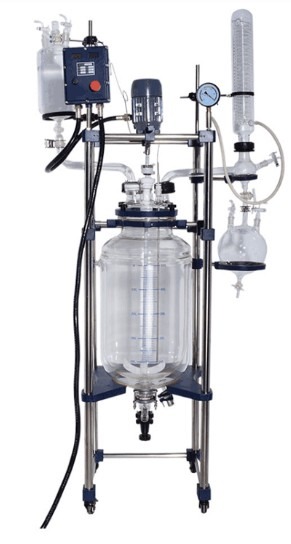
The jacketed glass reactor is designed for mixing and reaction of a variety of materials under particular adjustable vacuum and temperature conditions. The reaction lid has different operational ports allowing users to complete various tasks such as adding content at a controlled speed, add solids or powders to the vessel, measure the temperature of the material, or recover the distilled material and more.
Glass reactor systems are essential and used in the pharmaceutical and chemistry industries. The jacketed glass reactors are an indispensable piece of equipment used for refinement, distillation, homogenization, and extraction. Different cooling and heating liquids such as oil or water can be injected into the vessel through the interlayer of the jacketed glass reactor. These can also provide great mixing in the reactor under either sub-atmospheric or atmospheric pressure. The transparency of the glass allows you to monitor the entire reaction.
The design of the glass reactor was for synthetic reactions using different types of materials inside a vacuum and controlled environment. They consist of an inner vessel with either two jackets or one and a reactor that uses temperature differentials generated by a chiller to alter its internal environment.
Jacketed agitated reactors are designed to control the temperature of contents with a heating or cooling jacket around the reactor. The jacket allows the uniform exchange of heat between the fluid in the walls of the unit and that which is circulating. The filter base eliminates material transfers and reduces the loss of materials.
Features of 5L Glass Reactor
- PTFE rotary seal, high vacuum degree with a long useful life
- PTFE discharge valve, no leak/pollution to the solvent
- High-quality borosilicate glass with good physical and chemical attributes
Features of 10L Glass Reactor
- Stainless steel frame with strong support and hardness
- Double coil pipe inside the condenser
- AC induction motor, speed digital display constant, no spark, stable and safe
- Casters feature fixed brake making it stable and convenient
Features of the 50L Glass Reactor
- No electric brush, no spark, stable, safe and enables continuous working with constant rotate speed
- Glass part is constructed of borosilicate glass with excellent physical and chemical properties
- Inner core of stirring rod is constructed from stainless steel; military technology makes the workmanship exquisite with the high-proficiency operation
Safety Measures to Follow When Using Jacketed Agitated Glass Reactor
To effectively and efficiently use a jacketed agitated glass reactor, there are some safety measures you should follow to handle these vessels safely.
- Spark test the equipment
Do not use spark testers other than the ones recommended by the manufacturer. Spark testing is important in your maintenance technique and is used to find defects in the glass lining of the vessels. If this test is not performed properly, it can be quite destructive. Your personnel should be trained in how to inspect equipment and know how to identify potential areas of concern.
- Flush spills immediately
Exterior corrosion can lead to damage to the interior glass, so you should maintain the cleanliness of the entire vessel. You should not allow spilled chemicals to remain on any vessel exterior.
- Approve and monitor all products before adding to vessels
You should not charge materials through your nozzles without filtering the contents. Solids can impact the glass on the vessel or agitator blades and scratch the polish.
- Adhere to the minimal level requirements
You should operate the agitator with the appropriate liquid level, which is at the blade level. If the agitator is run when the fluid is below level, it can cause the shaft to experience excessive stress and runout in the seal and the upper end of the agitator.
- Close and secure all openings
Do not leave the manway cover open as you will risk it accidentally slamming shut and fracturing the glass. When it slams shut, you could injure yourself or other personnel
- Make sure vent is open
When you have a jacketed vessel, you should not keep the jacket vent closed. The vent is required to allow air to escape the jacket when it is being filled with liquid.
FAQ
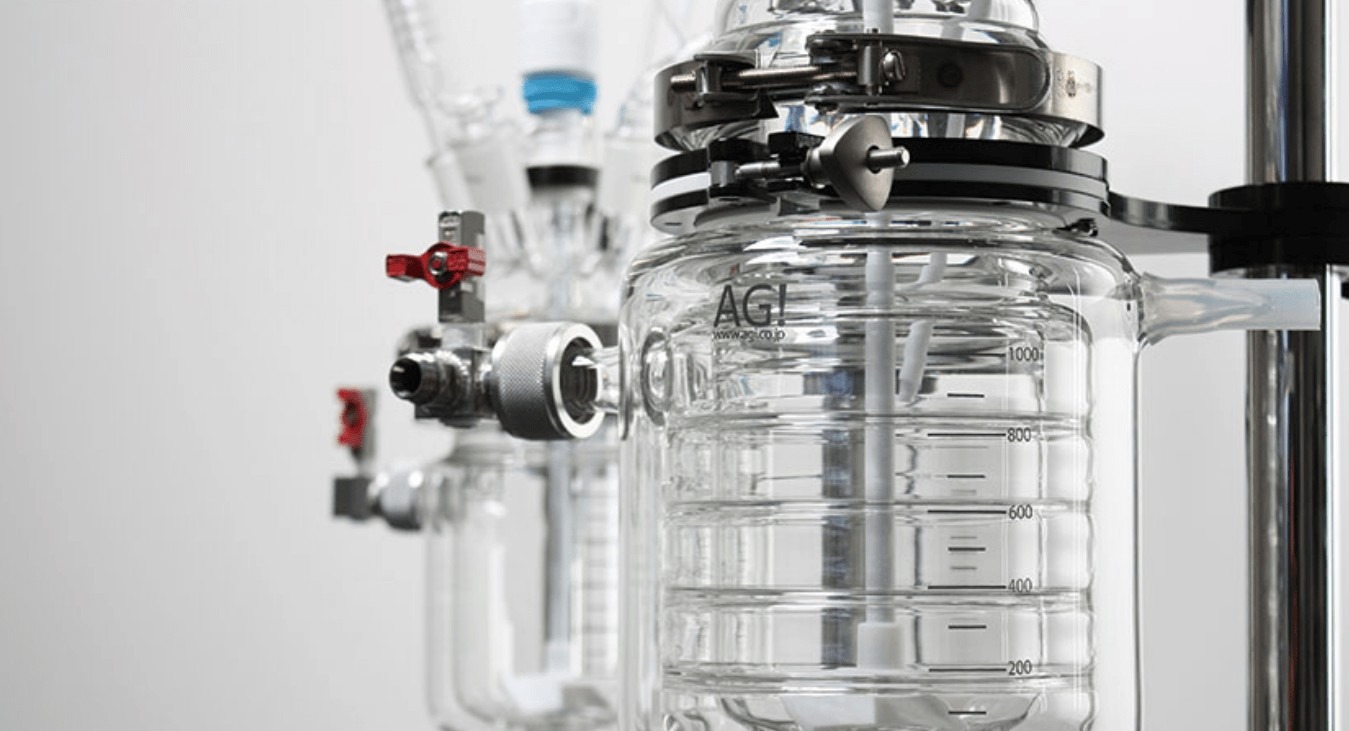
Q: How do you calculate the area of a reactor jacket?
A: You can take the diameter of your vessel for calculating the area times the length or distance of the jacket or channel. Area or normal area to the heat flow equals 3.14 x D2/4, and volume equals area x length or distance of channel or jacket.
Q: What is a reactor jacket?
A: A jacketed vessel is a container designed for controlling the temperature of its contents. It uses a heating or cooling jacket around the vessel by which a heating or cooling fluid is circulated.
Q: What is the difference between mixing and agitation?
A: Blending and mixing are the same actions, it’s the process of mixing two or more different components together. Agitation is a bit different but doesn’t mean there is more than one component present. Agitation just creates turbulence in your vessel.
Q: What is agitation speed?
A: Agitation means putting something into motion by either shaking or stirring to achieve mixing the components together. To measure the speed of agitation, you have to use the equation of Nq=Q/ND3
Conclusion
Heat transfer in stirred vessels is important as the process of fluid temperature in the vessel is one of the most important factors to control the outcome of the process. The agitated vessels are commonly used in food, petroleum, pharmaceutical, pulp, paper, and food industries. It is also used in coal gasification power plants.