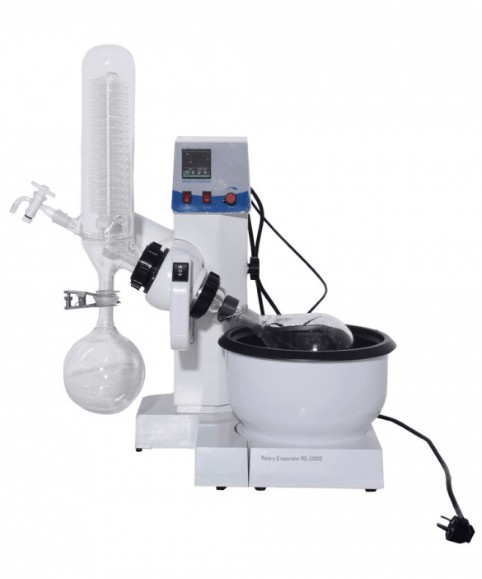
Rotary evaporators which are also known as “rotavaps” are used for removing solvents from a reaction mixture and can typically handle volumes up to 3 liters.
Roto-evaporation involves a flask that is mechanically rotated under vacuum. It is the action of rotation that speeds up the evaporation rate as the surface area increases. The vacuum is used for lowering the solvent’s boiling point, and to help separate the solvents from the desired compound.
They are commonly found in laboratories and allow these tasks to be carried out efficiently and effectively. The standard rotary evaporator is a piece of equipment that features a specialized water bath that is either heated in a crystallization dish or metal containers.
This water bath stops the solvents from freezing over the process of evaporation. The solvents are removed from the reaction mixture under vacuum. The solvent is then stored inside the condenser where it is later collected for disposal or reuse. Many of the laboratories use a basic water-aspirator vacuum with their rotary evaporators, which means the rotavaps are not suitable for water or air-sensitive materials.
In laboratories, a vacuum line, a membrane-pump or a circulation-bath are utilized as the primary source for this vacuum. A vacuum is typically applied to these setups as the solvents boiling points are usually much lower.
Since the flask rotates during the process of evaporation, it increases the surface area which speeds up the evaporation rates. The solvents are then collected inside the flask where they are disposed of in the correct manner. This method also helps to stop the targeted compound from overheating, for example, oxidation as much lower temperatures will be used in these processes.
Here is a list of the general rules for using rotary evaporators:
- The collection flask for the solvents must be properly emptied before use to avoid accidentally combining chemicals that are incompatible.
- The flask that contains a solution will be positioned on the rotavap. The bump trap performs the function of preventing the solution from spilling over and getting inside the condenser which would result in contamination.
- A Keck or metal clip is used for securing the bump-trap and the flask.
- The motor features a dial that allows the user to control the speed that the flask rotates at. The standard rotary evaporator uses a sparkless induction, variable-speed motor that typically spins at 0-220 rpm. These motors provide constant and high torque.
- To activate the aspirator vacuum, many models come with an on/off control that you turn on or off via a stopcock which is positioned over the condenser. The stopcock is also used at a later stage to vent the overall setup once the solvent has been removed.
- The flask is immersed in warm water by either lowering the flask directly into a water bath or raising the water bath up to the flask. Most of the models feature a handle that comes with a height-locking mechanism that will move the entire assembly (the condenser, motor, and flask) either down or up. In most cases, it is possible to adjust the condenser’s tilt. The temperature of the water bath should always be lower than the solvent’s boiling point. When it comes to common solvents in smaller amounts, the heated bath is usually not needed.
- Once the solvent starts collecting in the condenser it starts to drip down into a receiving flask. Some of the solvents like dichloromethane or diethyl ether are extremely volatile. These volatile solvents will evaporate once they reach the receiving flask where they are later discharged down a drain. To stop this process from occurring, either a dry-ice condenser is used or a cooling-bath at the receiver. In some cases, and added trap that contains liquid nitrogen or dry-ice will be positioned between the condenser and the vacuum. This is very important when membrane pumps are used as the vacuum source.
- As soon as all the solvents have evaporated, or whatever was desired at this stage, the vacuum releases. From here the spinning stops and the flask is lifted away from the water-bath.
- At the end of each process, the flask that receives these solvents must be emptied and the bump trap should be cleaned thoroughly.