Glass reactors are efficient chemical equipment because of their chemical and corrosion resistance and cleanability. However, their relatively low thermal conductivity puts them at a disadvantage. A device known as glass reactor jackets combats this disadvantage so that jacketed glass reactors can perform cooling and heating processes more efficiently.
Glass reactor jackets are used to circulate heat transfer liquids on both the interior and exterior of the jacket to increase or decrease the heat to and from the process. They have three primary functions which include:
- Modifying the jacket temperature
- Creating uniformity in the jacket temperature
- Stabilizing the jacket temperature
Generally, different types of glass reactor jackets can offer different deliverables depending on your needs and requirements. Below are a few examples of the types of glass reactor jacket design:
1. Conventional Jackets
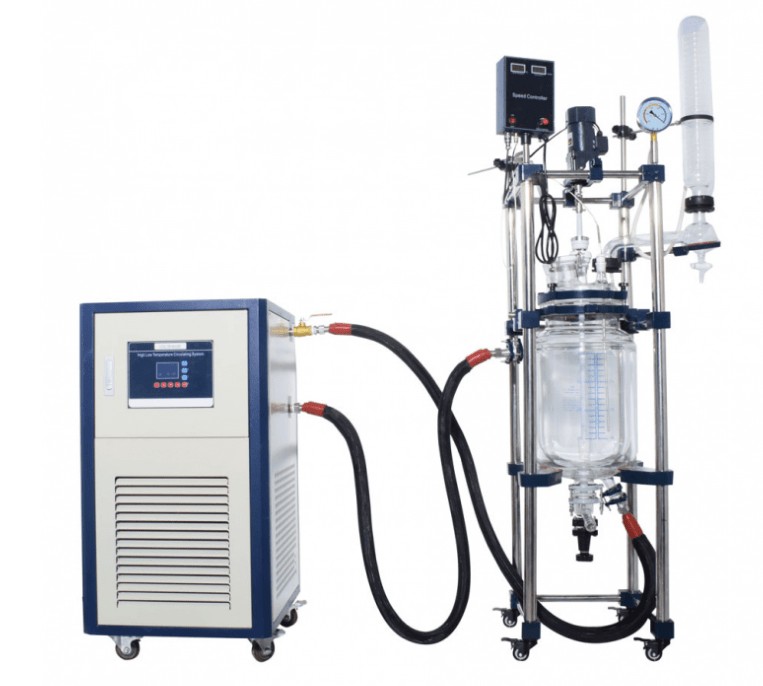
Conventional jackets, or also known as the single jacket, is an outer jacket that encases the vessel. It is the standard design for glass reactors and is also cost-efficient for buyers. Heat transfer fluid circulates the jacket and is injected through nozzles at high velocities. The temperature in the jacket is also regulated to control heating and cooling.
However, though it is the traditional type of jacket, it also comes with a few limitations. For example, the adjustment of fluid temperature takes a longer time, especially on larger vessels. Temperature variance can also take place between the bottom of the vessel and the side walls. Moreover, there is also the possibility of hot and cold spots forming at the inlet points of the jackets because of the temperature control valve. In short, this jacket does not control and distribute the temperature precisely.
2. Dimple Vessel Jackets
Dimple jackets are also cost-effective jackets composed of light-gauge metal. They can handle extra strength and durability because of its affixation to the vessel with spot or plug welds. However, can be subject to fatigue failure if they undergo rapid thermal cycling. This usually occurs if the jacket was quickly swapped from a heating process to a cooling process and vice versa.
3. Half-Pipe Coil Jackets
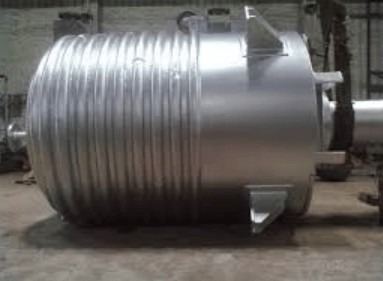
These jackets are made up of a welded half pipe that wraps the vessel. It circulates heat transfer fluid with increased velocity and turbulence in a circular path through coils. Heat transfer rates and film coefficients are consequently higher in comparison to conventional jackets.
The diameter of the pipe is where jacket pressure is concentrated, not in the height of the vessel. This makes the half-pipe coil jackets safer than conventional jackets as they can be operated at higher pressure levels. Usually, the standard operating limit for coil jackets is 450 PSIG at 500 degrees Fahrenheit.
This jacket is most compatible with multiple zone arrangements. In these versatile separate zones, pressure drops are reduced and heat transfer rates are high. Due to the shorter runs of coil pipes, fluid circulation is maximized as pumping energy is decreased. This set up can be useful for a process that heat steam or cool water media.
This jacket is also compatible with superimposed parallel circuits. It differs from the multiple zone arrangement because they can conduct heat transfers amongst incompatible media such as heating oil and cooling water. Circuits are divided into two or more zones depending on the size of your vessel and process requirements.
Just like the conventional jacket, coil jackets have their disadvantages, which is that they have to be welded to the vessel before it is glassed. On the other hand, conventional jackets can be installed at any time in the production process. It is also more pricy than conventional jackets but can decrease operating costs and offer better heat transfer rates.
4. Plate Coil Jacket
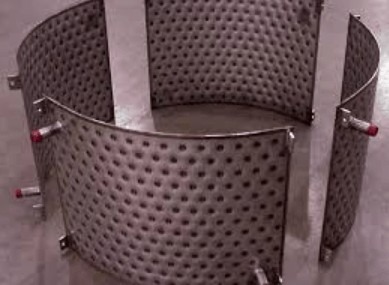
They are somewhat similar to dimple jackets in terms of installation but are strapped to the vessel and not affixed. This may be disadvantageous because it must be bonded adequately to avoid insulating gaps between the vessel and plate coil. It also as two layers of metal which include the shell of the vessel and the interior of the plate coil for heat to pass through.
Having a reactor jacket for your reactor will provide many benefits and advantages. However, each type of reactor jacket has its features and functions that can accommodate a wide range of needs and requirements. It is then important to identify exactly what you need to be accomplished so that you can purchase the reactor that is best suited to your needs.